Richard Levings, product manager American Augers, tells GDI about the company’s catch rig technology for HDD set-ups that are ideally suited to river crossings and lengthier bores that require a lot of time, machines and prep work on the trail pipe at the exit hole.
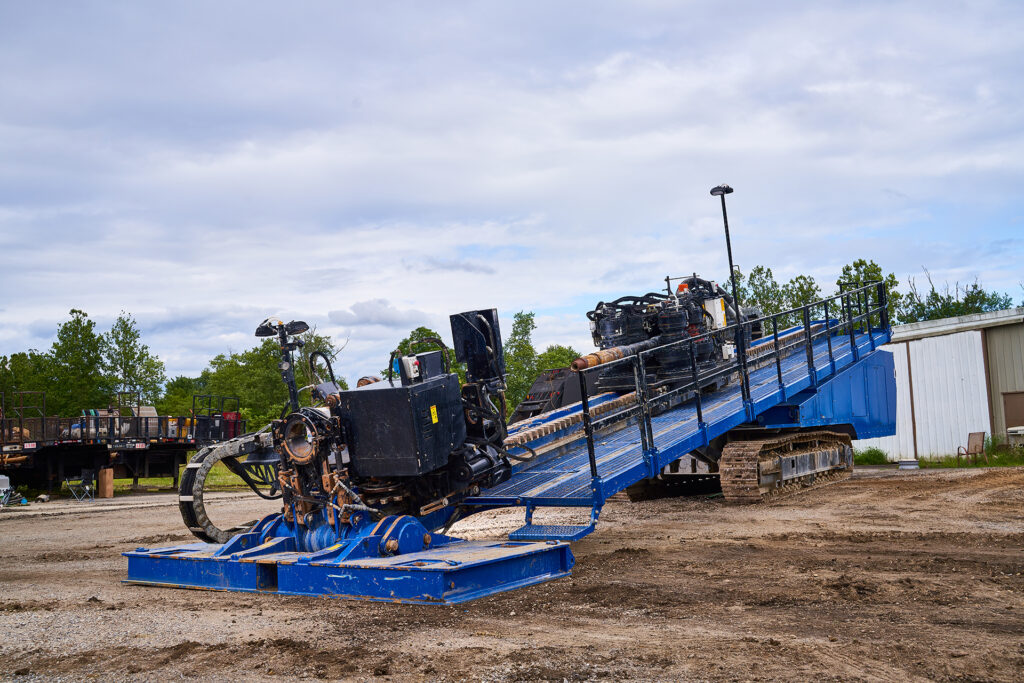
Since its inception in the 1970s, maxi horizontal directional drill rigs have steadily evolved to meet the changing needs of the industry. With technological advancements, these systems have gained broader acceptance and are now utilized in various applications across the globe.
For long-distance bores, contractors frequently need to operate maxi rigs on both sides of the installation to mitigate risks. This dual-sided operation allows operators to intersect pilot bores, manage fluid cleaning or pumping, assist with side pipe handling, and provide power assistance in challenging borehole conditions.
American Augers’ catch rig technology has successfully been used on HDD installations for multiple years. The system is ideally suited for river crossings and lengthier bores that require significant time, machines, and prep work on the trail pipe at the exit hole. The catch rig technology has significantly streamlined operations by eliminating the need for an external rotary swivel, which previously demanded considerable time and effort to install and uninstall, with each pipe joint added or removed.
Accelerates Operations
During the hole opening process, it is necessary to ensure a continuous string of drill pipe is in the hole. Depending on the project, the exit side of the bore will determine the method of managing the tail string as the borehole progresses.
Previously, contractors have been required to get creative when managing the drill pipe and the fluid flows on this exit side. Operators often spent significant time devising more efficient methods for executing procedures such as manual pipe connections, live rotating tail strings, and fluid swivels. Additionally, fluid containment, cleaning, and pumping all demanded careful attention and effort to ensure the bore progresses effectively.
To streamline the collaboration of two HDD rigs efficiently working together, HDD manufacturers have been prompted to develop new technology to make this process seamless and efficient. With a focus on reducing labor and minutes per connection, manufacturers like American Augers have risen to the challenge, introducing new patented technology.
With efficiency in mind, catch rig technology uses an additional HDD rig on the exit side (often already present as an intersect rig) to hydraulically make and break each pipe added or subtracted. To do this, the rotary system had to be capable of being put in neutral or enabled by a finger touch on the control screen of the drill. By enabling the rotary system, the catch rig can thread the new pipe on or break the pipe joint depending on the direction of the drill string movement. Using the rig wrenches greatly mitigates risks and ensures an efficient connection. Once the connection has been made, the rotary is put in neutral, thereby not interfering with the rotary power of the drive rig.
As a bonus, the rotary fluid swivel used on normal HDD rig operations can be used to pump fluid from the exit side, eliminating the need to insert an external swivel for each new joint added or subtracted. This greatly improves the efficiency of pumping fluid from the exit side when fluid flows to that side of the bore.
Mitigates Risk
A catch rig eliminates the need for a swivel on the front of the rotary on the exit side rig. Typically, this swivel has a fluid hose connected to it, and operators often pump fluid from the exit side, depending on which side of the bore the fluid is running to, to reclaim on both sides and pump back.
Keeping the pipe moving during the hole opening and swabbing phase of the boring process is key to reducing risks and costs associated with solids in the borehole. Using a catch rig with this patented technology, contractors experience significantly reduced dwell time in the fluid stream, which keeps the solids in suspension, making it easier to move from the hole to the surface. Another major benefit is reduced days required to complete the total project. Every additional day on a project increases risks and costs.
Boosts Efficiency
Contractors are looking for ways to complete projects for less money and fewer people. Labor challenges are one of the most difficult things they have to deal with daily. This catch rig technology helps contractors be more efficient, reduces the time spent on projects, and saves money.
While specific time trials and case studies are still forthcoming, industry experts estimate that catch-rig technology could conservatively save contractors approximately 15 minutes per pipe connection. For a 3000ft bore requiring 100 connections of 30ft pipe, this translates to significant time savings. Additionally, the streamlined process eliminates the need for a swivel and reduces the number of personnel required for each connection. With catch-rig technology, these tasks can be completed in under two minutes with just two operators.
Incorporating catch-rig technology into the HDD process significantly enhances jobsite efficiency. Although a second HDD machine may increase costs, many contractors already own or can rent additional units. By integrating a catch rig system, contractors can dramatically boost crew productivity and performance, positively impacting both the HDD process’s effectiveness and the contractor’s bottom line.